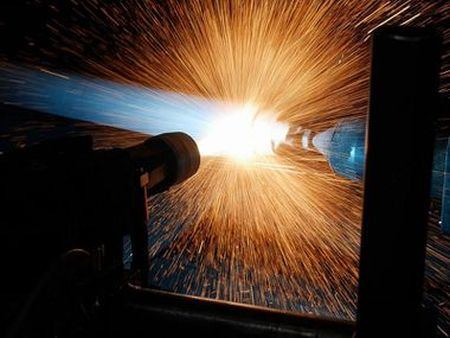
VLAMSPUITTECHNIEKEN
In flame spraying (also known as thermal spraying) we apply a coating to a part to ensure that it performs better. The different flame spraying techniques use various metals and alloys, which are sprayed in powder or wire form depending on the specific flame spraying technique.
APS
Atmospheric plasma spraying (APS) is the process of melting a powdered material by heating an electric arc with ionized gas (a plasma). Due to the heat (± 20,000˚C) and the good conductivity of the flame, this technique is ideal for giving a sprayed layer strong adhesion and homogeneity. The high temperature in this process also means that there are few restrictions on spray materials.
HVOF
HVOF stands for the term High Velocity Oxygen Fuel. In this spraying process, a powder is axially injected into a chamber where a gas flame burns constantly under high pressure. The fine powder particles are heated in the gas stream and fired onto the surface of the workpiece at high speed. As a result, the powder particles together form a dense coating with a very high adhesive strength.
Applications & Coatingmaterials
- Superalloys like Stellite, Tribaloy, Colmonoy and Inconel
- Iron based alloys like AISI 316L or chroomsteel
- Carbides and cermets like chroom- of tungstencarbides
- Bonding layers like NiAl or MCrAlY’s
- Chemical resistant coatings (corrosie)
- High temperature applications (oxidation)
- Wear resistant (adhesive, abrasive, erosive)
- dimensional recovery
ELEKTRIC WIRE SPRAYING
Electric wire spraying is the process of drawing an electric arc of approximately 4000˚C between two metal wires, causing them to melt. The molten material is atomized with compressed air or nitrogen. Electric wire spraying provides a microporous and lamellar layer that has good adhesion with a high yield. This technique is widely used for repair purposes.
Coatingmateriales
Applications
- Iron base alloys such as stainless steel or chrome steel
- NiCkelbase alloys such as NiAl
- Aluminium, zinc and mixtures
- Superalloys such as Inconel of Stellite
- Bearingmaterials such as babbitt or aluminiumbronze
- Bonding layer
- Wear resistanced
- Dimension recovery
- Corrosion protection
OXY-FUEL WIRE SPRAYING
In oxy-fuel wire spraying, a metal wire melts in a flame of 2,800 to 3,200 ° C. Compressed air then causes the molten material to atomize on the work surface. This technique is suitable for spraying various metals and alloys and is widely used for repair work or corrosion protection.
Coatingmaterials
Applications
- Bearing materials like babbit, brass end aluminiumbronze
- Electrical conductive materials like tin, copper and zinc
- Ceramics such as aluminum oxide, chromium oxide and zirconium oxide
- "Self-lubricating" topcoat or coatings with running-in properties
- Wear resistance and corrosion resistance (ceramic)
- Elektromagnetic protection
OXY-FUEL POWDER SPRAYING
Oxy-fuel powder spraying is a process in which metals, alloys and metal compounds in powder form are sprayed in a flame up to 3,200 ° C. The heat ensures that the material is melted, after which we can spray the material. Autogenous powder spraying has a "cold" and a "warm" variant. In the cold variant, the temperature of the base material does not get hotter than 200 ° C, so that no structural change and deformation can take place. This makes this technique extremely suitable for repair applications.
CoatingmaterialS
Applications
- Nikkelbased alloys
- Cr-steel en strainless steel alloys
- Ceramics such as aluminum oxide, chromium oxide and zirconium oxide
- Hardwearing materials such as Nickel Graphite or AlSi Polyester
- Fusing alloys such as NiCrBSi, CoNiCrBSi, WC-NiCrBSi
- Thermally insulating coatings
- "Self-lubricating" coatings or coatings with running-in properties
- Wear and corrosion resistant coatings (ceramic)
- Impact and shock resistant melted-in coatings